Wine-fueled thoughts on reinventing the store
Wine-tasting conversation: What do retailers have to say about evolving store operations, automation of back-office operations and supply chain?
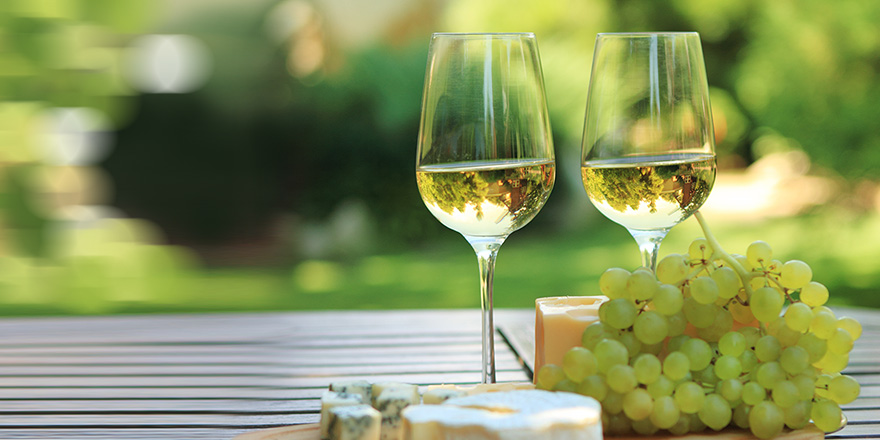
Visiting sunnier climes while travel restrictions are in place might be difficult but some of the UK’s most respected retailers managed a tour of Spain recently.
“How?” I hear you ask.
They joined Software AG and The Drink Talking for an online wine-tasting adventure, learning about some of the 74 wine regions of Spain but also taking a little time out to discuss the changes taking place in the retail industry.
As well as tips on tasting wine – more complicated that I had realized – and sampling accompanying Spanish cheeses, the retailers who joined were asked perspectives on the near future of their industry. Topics spanned evolving store operations, automation of back-office operations and supply chain, and were primed with a short video.
Their comments were interesting and definitely worth writing about. Here are some of the highlights:
- Stores are definitely becoming multi-functional. There was wide agreement that the role of store associates is expanding, and that technology will need to play a part in augmenting their expertise. And, while employees are a significant expense for retailers, they also have potential to become a major competitive edge.
- Digital upstarts are not held back by legacy. New digital-first entrants have a significant advantage because they lack the legacy systems associated with traditional business. British online retailer Asos.com was mentioned as an example; it has just 20 years of heritage in its systems and processes but is also incredibly customer focused. This suggests, perhaps. that younger retailers may benefit culturally as well.
- Seamless experiences are important to the customer. This was no surprise and it is great to hear it acknowledged by retailers striving to achieve these journeys.
- Supply chains need further defragmentation. Retailers live by the efficiency of their supply chains. Even after multiple years of investment, delivering against ever-evolving customer expectations in a profitable way remains challenging.
- Technology cannot solve all problems. Although this was said to be true, it was also acknowledged that most problems cannot be solved without technology. It was also acknowledged that the business’s ambition can often outpace the capacity of its technology team to deliver solutions.
The event was a great success with guests expressing appreciation for different Thursday evening – learning something about wine while sharing viewpoints on retail technology.
Software AG is equally grateful to guests for attending a fun format we are likely to use again. You can view the thought-provoking video yourself here.
And see below how Software AG’s integration, business process transformation and IoT technologies can help you reinvent the store.